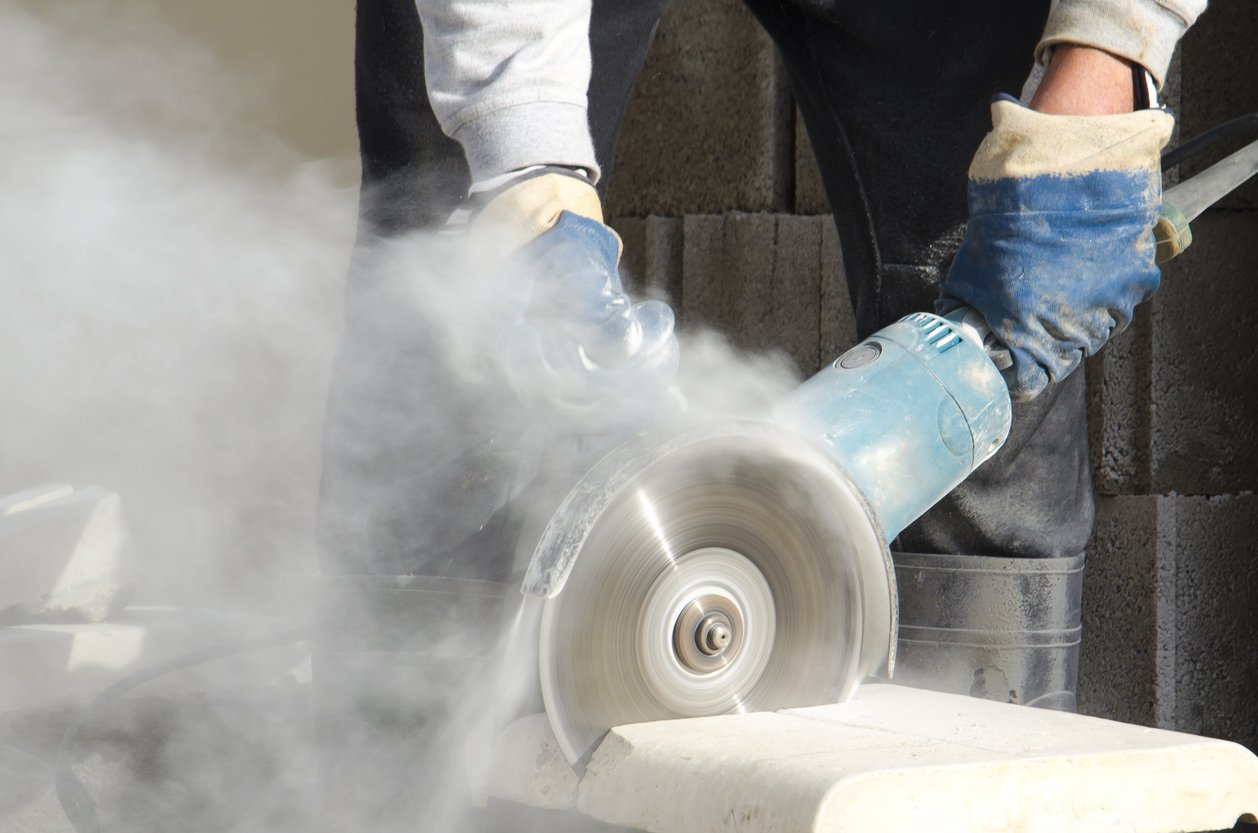
When it comes to working in construction, safety should always be at the forefront of everyone’s mind.
It doesn’t matter what task you’re doing – from working at height to handling heavy machinery, to something as mundane as filling out paperwork – every project brings its own challenges and risks. But while we often focus on the obvious hazards, there’s one that’s a bit more hidden, yet just as dangerous. And that’s respiratory risks.
Dust, fumes, gases, and vapours are a common part of many construction tasks. According to the Health & Safety Executive (HSE), 12,000 deaths from lung disease each year are estimated to be linked to past exposures at work. Left unmanaged, these invisible hazards can cause serious long-term health problems down the line.
In this blog, we’ll break down what respiratory risks in construction are, why they matter, and the practical steps you can take to keep your workforce safe.
When we talk about respiratory risks in construction, we’re referring to any hazards that can damage the lungs, airways, or the ability to breathe. The biggest culprits are:
The particles don’t just disappear: they linger in the air long after the work’s finished. Breathe them in, and they can cause a range of health issues, from short-term irritation to long-term, life-threatening diseases like chronic obstructive pulmonary disease (COPD), occupational asthma, silicosis, and even lung cancer.
According to the HSE, in the UK, there are currently 20,000 new cases each year of work-related breathing or lung problems (averaged over the last three years).
It’s easy to think of safety in construction as primarily about preventing accidents like falls, cuts, and collisions. But health risks can be just as severe, even if they’re slower to appear.
Respiratory diseases often develop over time, sometimes after decades of exposure. By the time symptoms show, the damage may already be done. That’s why prevention is so critical.
There’s also a legal angle. Under the Control of Substances Hazardous to Health (COSHH) Regulations 2002, employers have a legal duty to assess and control exposure to substances that can cause ill health. Failure to do so can result in hefty fines, legal action, and reputational damage.
But even moreso, it’s about creating a culture of care.
We say it a lot, but it’s true: your people are your greatest asset. Keeping them healthy doesn’t just help you stay on the right side of the law. It boosts morale, reduces absenteeism, and helps you build a reputation as a responsible, trustworthy business.
So, how can you tackle respiratory risks in construction head-on? Let’s take a look.
First things first: you can’t manage what you don’t know. A thorough risk assessment is your starting point.
Look at the tasks your team carries out daily:
Don’t just focus on the obvious. Think about the entire work environment, too:
Be methodical. Involve your team. And remember, the more detailed your risk assessment, the better placed you’ll be to implement effective controls.
Once you’ve identified the risks, it’s time to tackle them. The hierarchy of controls is a simple but powerful tool for managing risks, with a clear order of priority:
Many sites jump straight to masks and respirators, but relying on PPE alone isn’t enough. After all, a face mask can only do so much!
When it comes to controlling respiratory risks in construction, the right equipment makes all the difference. Here are a couple of items you can use to make the job safer and easier:
Equipment is only effective if it’s well-maintained. Make sure to take part in regular inspections, servicing, and filter replacements to keep your employees safe.
Knowledge is power, and when it comes to respiratory risks, it can be life-saving.
Your team needs to understand:
Training should be part of your induction process for new starters and refreshed regularly for all staff. This is where Health & Safety Awareness training can make a real difference. It helps your team understand not just the risks they face, but how to work safely, confidently, and in line with best practices.
Managing respiratory risks in construction isn’t a one-and-done exercise. It’s an ongoing process.
Regular site inspections and air monitoring (where needed) can help you spot problems early, make adjustments, and make sure your controls remain effective.
Keep communication open. Encourage workers to report any issues, near misses, or concerns. Remember, your team’s on the front line – they’re the ones who will see if anything’s wrong first, so their feedback is invaluable.
Finally, creating a culture where safety is everyone’s business makes all the difference. Real change happens when:
It’s not just about rules and regulations. By showing that you care about your team’s health, not just today, but for years to come, you build trust, loyalty, and a stronger business.
This is where SSIP certification can really help demonstrate your commitment. It’s a recognised standard that shows you’re serious about Health & Safety. If you’re tendering for contracts or working with larger clients, having that certification can give you a real competitive edge. It also helps with:
Give your team the knowledge they need to stay safe. We offer a bunch of online training courses, like our Health & Safety Awareness course, which delves further into this topic and keeps your employees informed on how to protect themselves and others!
And, with our SSIP certification, you can demonstrate your commitment to Health & Safety compliance with a nationally recognised certification. Get in touch with us today to see how Smas can keep you safer at work!