Understanding behavioural hazards in the workplace
Your business’s Health & Safety procedures are the driving force behind reducing risks within your business’s day-to-day tasks. But behavioural safety hazards are something that you should be aware of and minimising within your workforce.
There’s no one reason why behavioural safety hazards can become a problem. It could be that workers feel new rules or precautions are unnecessary or delay tasks, so they don’t feel the need to stick to the guidelines. Or it could be because a workforce or organisation becomes careless with their safety procedures and culture over time.
Whatever the reason, site managers and the general team need to be aware of areas where issues could arise, and how to solve the problems when they do.
What is behavioural safety?
Behavioural safety focuses on the human actions that contribute to workplace incidents and accidents. It recognises that even with the best safety procedures and equipment in place, people can still make errors or take shortcuts that put themselves and others at risk.
A robust behavioural safety policy aims to understand why these unsafe behaviours happen, and put measures in place to encourage safer working practices. It’s about creating a culture where everyone takes responsibility for their own safety and the safety of their colleagues.
Good behavioural safety works hand in hand with traditional hazard control methods. The point isn’t to blame individuals, but to recognise and address the human element of risk. This way, you can identify specific patterns and issues to better promote a positive safety culture.
Behavioural hazards examples
Behavioural hazards are unsafe actions (or inactions) by workers that can lead to accidents, injuries, or near misses. These hazards can come from various factors, including, but not limited to:
- Complacency
- Time pressures
- Lack of awareness
- A general disregard for safety rules
Here are some examples of behavioural hazards in the workplace.
Lack of adherence to PPE requirements
This includes not wearing required personal protective equipment (PPE) such as safety glasses, hard hats, gloves, or harnesses.
For example, a construction worker might skip wearing a harness because they’re only working at a low height “for a minute”. Or a lab technician might not wear gloves because they think they’re handling a harmless chemical.
Taking shortcuts
Rushing to complete a task can lead to taking shortcuts that bypass safety procedures. For instance, an electrician might not properly isolate power before working on a circuit, or a delivery driver might speed to save time or fulfil a quota.
Failure to follow procedures
Ignoring established safety protocols, such as lockout/tagout procedures, confined space entry protocols, or machine guarding requirements, is a major behavioural hazard.
Distracted working
Operating machinery or performing tasks while distracted seriously increases the risk of accidents. This includes:
- Being on your phone
- Conversations with colleagues whilst performing dangerous tasks
- Over-tiredness or sickness leading to drowsiness or nausea
- Eating or drinking whilst working
A forklift driver texting while driving is a clear example.
Poor housekeeping
A cluttered or disorganised work environment can create trip hazards, block emergency exits, and contribute to other accidents. Leaving tools or materials lying around is a common behavioural hazard.
Inadequate training or understanding
If workers aren’t properly trained on how to perform tasks safely or do not understand the risks involved, they’re more likely to engage in unsafe behaviours.
A great way to limit behavioural safety hazards is to make sure, right from the get-go, that everyone understands the risks involved.
Complacency
When you’ve worked somewhere for a while, it’s easy to get complacent about routine tasks. But this can lead to a lapse in attention and an increased risk of errors. A worker who’s performed the same task hundreds of times might become less vigilant and more likely to make a mistake.
Failing to report hazards
If you don’t report near misses, incidents, or potential hazards, you’re missing out on vital data that help identify and correct unsafe conditions or behaviours.
This could be due to fear of criticism, a belief that nothing serious happened, or a lack of awareness of a company’s reporting procedures.
All of these examples of behavioural hazards contribute to a higher risk of accidents.
Causes of behavioural safety risks
There are many factors that can contribute to behavioural hazards in the workplace. So, it’s important to understand what these causes are so you can develop effective solutions to stop them from happening again.
Here are nine things to keep an eye out for…
1. Time pressure and workload
Tight deadlines and heavy workloads can pressure workers to take shortcuts or skip safety steps to complete tasks quickly.
2. Lack of awareness or training
If workers aren’t adequately trained on safe working procedures or aren’t aware of the potential hazards associated with their tasks, they’re more likely to engage in unsafe behaviours.
3. Poor safety culture
A workplace culture that doesn’t prioritise safety, or tolerates unsafe behaviours, can contribute to a higher incidence of behavioural hazards. This impacts the overall behavioural safety of the organisation.
4. Inadequate supervision
Insufficient supervision can lead to workers feeling that they can get away with unsafe practices.
5. Complacency and habit
Repeatedly performing the same task can lead to complacency and the development of unsafe habits. This can be a significant behavioural hazard.
6. Stress and fatigue
Stress and fatigue can impair judgment, reduce concentration, and increase the likelihood of errors and unsafe behaviours.
7. Lack of motivation or engagement
Workers who aren’t motivated or engaged in their work may be less likely to follow safety procedures.
8. Communication issues
Poor communication between workers, supervisors, and management can contribute to misunderstandings and unsafe practices. This also has a knock-on effect on the behavioural safety policy of the organisation.
9. Individual attitudes and beliefs
Some individuals may be more inclined to take risks or might not believe that safety rules are necessary. Addressing these individual attitudes can be a challenge, but it’s an important one if you want to make sure everyone stays safe.
Understanding these behavioural hazards and their root causes is the first step in creating a safer work environment.
Something along the lines of the above statement is often true when you’re looking to change a policy or introduce new steps in your health and safety procedure. These habitual procedures are even more difficult to introduce when the task one is carrying out becomes either more difficult or longer to complete due to the changes. For example, someone who has previously not been required to wear gloves is now asked to wear protective gloves, but they impede his ability to complete the task due to the bigger size and lack of movement.
When implementing a change in equipment or procedures you should make sure you sell it to your workforce. Most of the updated equipment’s marketing will be around the benefits of it, how it works and what risks it will reduce and/or stop. This should be relayed to those who will be required to use it going forward so they can see why you’re making the changes.
Changing the behavioural habits
Managing behavioural risks is a challenge that all businesses face, and changing existing procedures can be extremely difficult.
Often, these behaviours become habits which can be extremely difficult to change.
To help you work through it, we’ve put together 10 steps that your business can take to stop bad habits from creeping into the workplace.
1. Take a no-tolerance stand
The best and most effective way to stop behavioural risks is to make sure you’ve got a no-tolerance stance on your Health & Safety procedures.
Make it clear that, if anyone’s found breaking rules, they’ll be removed from the work environment. This’ll reinforce your stance to other employees, and help stop bad habits forming early on.
2. Sell the change to your staff
Make sure your staff are aware of the reasons behind the changes in procedure or equipment. If they know why you’re implementing new policies, they’ll understand the risks that come with not following them. Use case studies (both success stories and ‘here’s what not to do’ stories) from other businesses to emphasise and sell your point.
3. Create a safety-first culture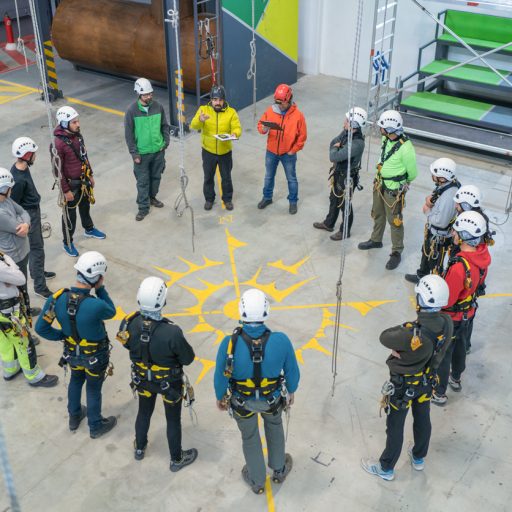
Creating a culture within your workplace takes time. But, once it’s in place, you’ll find it’s much easier to manage changes in the long term. Build a culture of community and mutual respect. People are more likely to be safety conscious if they know that they’re also looking out for other people – not just themselves.
Once this culture has been created, your task becomes much easier, as the safety standards will now be pushed from within teams, not from an unseen figure at the top of the business.
4. Lead by example
Management and supervisors must visibly demonstrate their commitment to safety by consistently following all safety procedures and best practices. This sets the tone for the entire organisation and reinforces the importance of safe behaviours. If leaders are seen to disregard safety rules, employees are likely to follow suit.
5. Reinforce positive behaviour
Recognising and rewarding employees who consistently demonstrate safe behaviours is essential. This can be done through verbal praise, written acknowledgements, or other forms of recognition. Focusing on positive reinforcement is more effective than just punishing unsafe actions.
6. Regular communication and engagement
Open and frequent communication about safety is vital. This can involve regular safety meetings, toolbox talks, or informal discussions. Encourage employees to ask questions, share concerns, and provide feedback on safety procedures.
7. Empower employees to speak up
Create a safe environment where employees feel comfortable reporting hazards, near misses, and unsafe behaviours without fear of reprimand. Encourage them to actively participate in safety initiatives and offer suggestions for improvement.
8. Provide regular refresher training
Regular refresher training helps to reinforce safe work practices and address any knowledge gaps. This is particularly important for tasks that aren’t performed as often, or that involve new equipment and procedures. This training should also cover behavioural hazards and how to avoid them.
9. Make safety visible
Use visual cues, like posters, signs, and labels, to remind employees of safety procedures and potential hazards. Make safety a visible and ongoing part of the work environment.
10. Measure and track progress
Monitor the effectiveness of interventions by tracking key metrics, like incident rates, near misses, and safety observations. Use this data to identify trends, evaluate the impact of changes, and refine your approach to behaviour change.
A step-by-step guide to improving behavioural safety:
So, to sum up:
- Review your current processes and/or equipment and decide on the areas you want to improve. Consider using previous accident, incident and near-miss reports to help you identify areas of improvement.
- Once you’ve reviewed your procedures, select one or two key areas that can be improved. A complete overhaul of all procedures will be tougher for employees to follow and digest.
- Begin developing your communication strategy. How are you going to present the changes to your employees? Can you use examples from your business?
- Implement your changes with a few initiatives such as:
- Colleague observation studies
- Regular inspections from senior management
- Regular bite-sized training or refresher classes
- Reward those who excel with positive feedback and reinforcement
- Include behavioural risks within your risk assessments
- Monitor the changes and make improvements where necessary. Be open with your employees and ask for their feedback.
Create a safe workplace with support from Smas Worksafe
If you’re unsure of the best practices for creating a safe workplace, we’re here to help.
We’ve made it our mission to boost industry standards across the UK through SSIP certification, helping businesses like yours demonstrate their commitment to Health & Safety. We also offer a selection of online, CITB-approved training courses, including:
- Site Supervisor Safety Training Scheme (SSSTS)
- Site Supervisor Safety Training Scheme Refresher (SSSTS-Refresher)
- Site Management Safety Training Scheme (SMSTS)
- Site Management Safety Training Scheme Refresher (SMSTS-R)
- Health & Safety Awareness (HSA)
Simply get in touch today to learn more! Our friendly, in-house team is always happy to talk you through how we do things, and find a system that helps your business most.