News
Here you’ll find a selection of the latest updates from the various industries we work with and of course, there’s content on workplace safety, supply chain management and SSIP, along with company updates from SMAS Worksafe.
Always striving to continue our professional development, we also often share articles which we have put together, with the specific purpose of sharing valuable insight that could benefit your business.
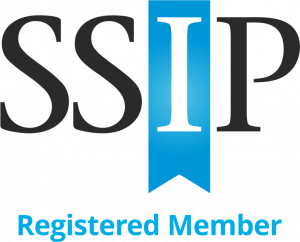
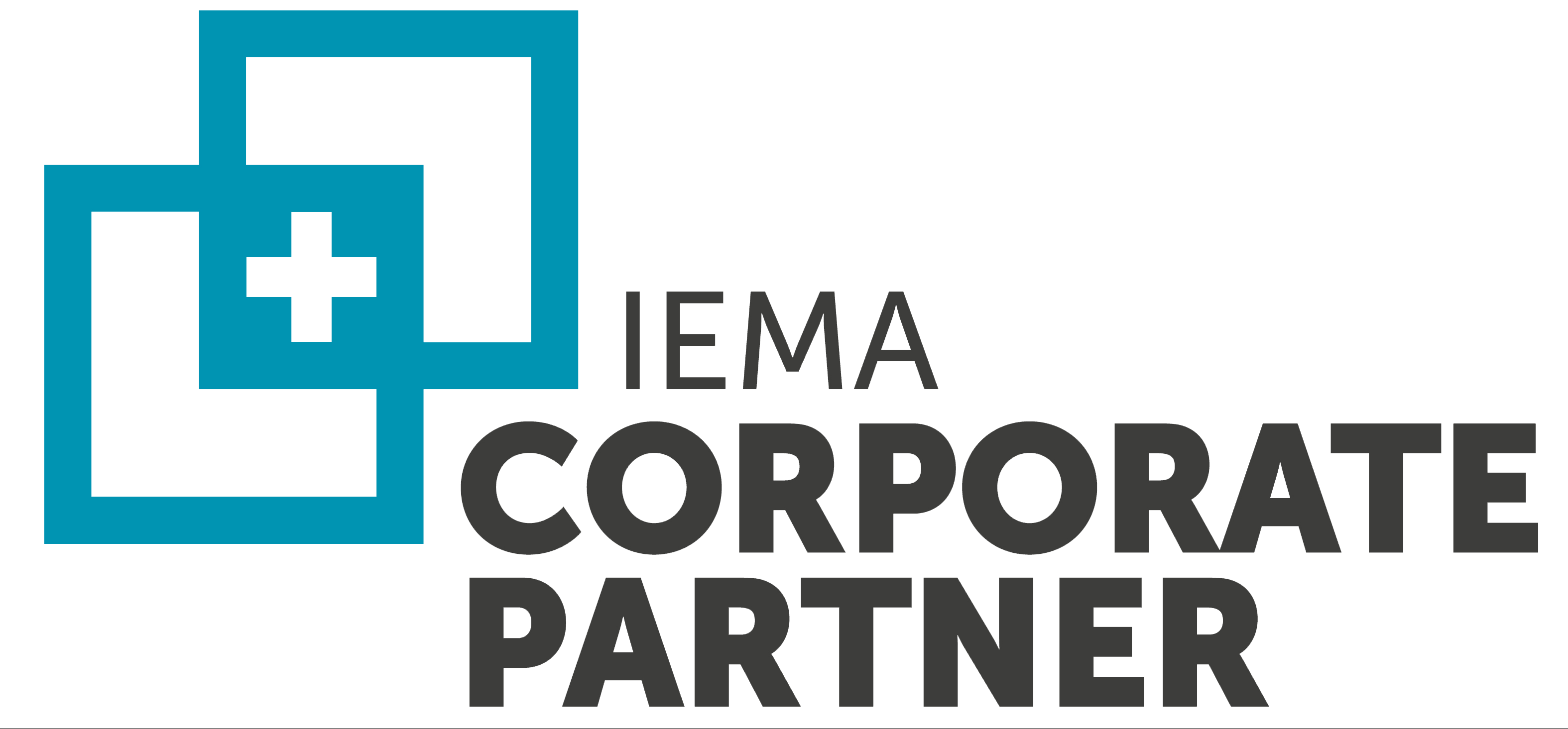
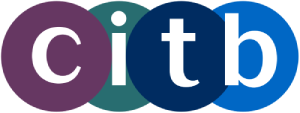
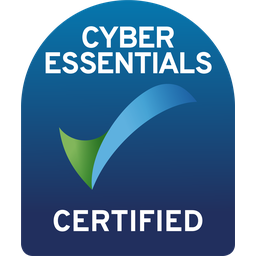
All Uncategorized News Worksafe PQQ Worksafe Supply Chain Quality Environment Health & Safety Modern Slavery Anti-Bribery & Corruption Training